Innovating Oil & Gas Piping Systems with HDPE Technology
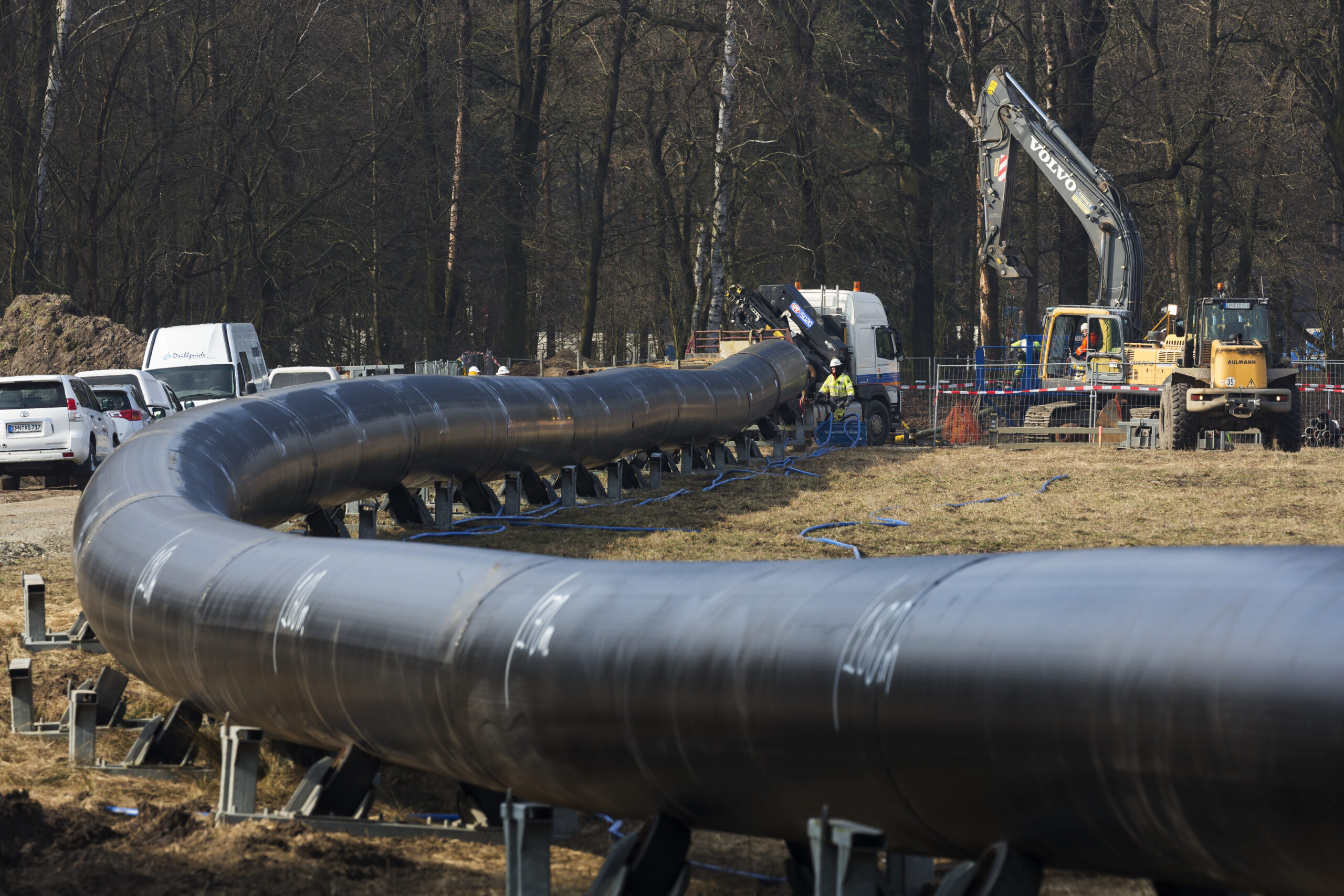
The oil and gas industry relies heavily on piping systems for the transportation of crude oil, natural gas, and various other fluids. These piping systems must withstand extreme conditions, including high pressures, temperatures, and exposure to corrosive substances. The integrity and reliability of these pipes are critical to ensuring the safe and efficient operation of oil and gas facilities, as well as minimizing environmental risks.
Traditionally, the oil and gas industry has relied on metal pipes, such as carbon steel and stainless steel, for their piping needs. While these materials have proven their strength and durability over the years, they also have limitations that can impact the overall performance and sustainability of oil and gas operations.
HDPE’s benefits in oil and gas applications
High-density polyethylene (HDPE) has emerged as a game-changing technology in the oil and gas industry, offering a range of benefits that address the limitations of traditional piping materials.
One of the key advantages of HDPE pipes is their exceptional resistance to corrosion. Unlike metal pipes, which can corrode and deteriorate over time due to exposure to moisture, chemicals, and other corrosive substances, HDPE pipes are inert and do not react with most chemicals. This corrosion resistance translates into longer service life, reduced maintenance costs, and improved system reliability.
HDPE pipes also offer excellent resistance to abrasion and wear. In oil and gas applications, the transportation of fluids often involves the presence of abrasive particles, such as sand and sediment. These particles can erode the interior of metal pipes, leading to leaks and failures. HDPE pipes, with their smooth interior surface and tough material properties, can withstand the abrasive effects of these particles, minimizing wear and tear and extending the life of the piping system.
Another significant benefit of HDPE pipes in oil and gas applications is their flexibility and ease of installation. HDPE pipes are lightweight and can be easily bent and shaped to conform to the contours of the terrain. This flexibility allows for the creation of long, continuous pipeline runs with fewer joints and connections, reducing the potential for leaks and simplifying installation. The lightweight nature of HDPE pipes also makes them easier to transport and handle, reducing installation time and costs.
HDPE pipes also offer improved flow characteristics compared to metal pipes. The smooth interior surface of HDPE pipes reduces friction and turbulence, allowing for more efficient fluid flow. This increased flow efficiency can result in lower pumping costs, reduced energy consumption, and improved overall system performance.
Comparing HDPE with traditional materials in oil & gas
When compared to traditional materials used in oil and gas piping, such as carbon steel and stainless steel, HDPE pipes offer several advantages. In terms of corrosion resistance, HDPE pipes outperform metal pipes, as they do not rust, corrode, or degrade when exposed to moisture, chemicals, or other corrosive substances. This superior corrosion resistance eliminates the need for costly corrosion protection measures, such as cathodic protection or protective coatings, which are often required for metal pipes.
HDPE pipes also have a lower thermal conductivity compared to metal pipes, meaning they provide better insulation and minimize heat loss. This thermal insulation property is particularly valuable in oil and gas applications where maintaining the temperature of the transported fluids is critical for process efficiency and energy conservation.
In terms of cost-effectiveness, HDPE pipes offer long-term savings compared to metal pipes. While the initial cost of HDPE pipes may be higher than some metal alternatives, their longer service life, reduced maintenance requirements, and improved operational efficiency result in lower lifecycle costs. The use of HDPE pipes can also lead to reduced downtime and improved system availability, as they are less prone to leaks, failures, and corrosion-related issues.
Safety and environmental considerations
The use of HDPE pipes in oil and gas piping systems also has significant safety and environmental benefits. HDPE pipes are non-toxic and do not leach chemicals into the surrounding environment, reducing the risk of soil and water contamination. In the event of a leak or spill, HDPE pipes minimize the potential for environmental damage, as they do not corrode or degrade, preventing the release of harmful substances.
HDPE pipes also contribute to improved safety in oil and gas operations. Their leak-free performance, achieved through advanced fusion welding techniques, reduces the risk of fluid leaks and the associated fire and explosion hazards. The flexibility and impact resistance of HDPE pipes also make them less susceptible to damage from ground movements, seismic activity, and other external forces, enhancing the overall safety and integrity of the piping system.
HDPE pipes support the oil and gas industry’s efforts to reduce its environmental footprint. The production of HDPE pipes requires less energy compared to the manufacturing of metal pipes, resulting in lower greenhouse gas emissions. HDPE pipes are also recyclable, contributing to the circular economy and reducing waste in the oil and gas sector.
As the oil and gas industry continues to evolve and face new challenges, the adoption of HDPE piping technology will play an increasingly important role in driving innovation and sustainability. The integration of HDPE pipes with advanced monitoring and sensing technologies, such as fiber optic cables and smart sensors, will enable real-time monitoring of pipeline integrity, leak detection, and predictive maintenance. These advancements will further enhance the safety, efficiency, and environmental performance of oil and gas piping systems.
HDPE technology is revolutionizing the oil and gas industry by providing a superior alternative to traditional piping materials. The benefits of HDPE pipes, including exceptional corrosion resistance, abrasion resistance, flexibility, and cost-effectiveness, make them an ideal choice for the demanding conditions of oil and gas applications.
The use of HDPE pipes not only improves the operational efficiency and reliability of oil and gas piping systems but also contributes to enhanced safety and environmental sustainability. By minimizing the risk of leaks, corrosion, and environmental contamination, HDPE pipes support the industry’s efforts to reduce its environmental impact and maintain the highest standards of safety.
As the oil and gas industry continues to embrace innovation and adapt to new challenges, the adoption of HDPE piping technology will be a key driver of progress. By investing in this advanced technology, oil and gas companies can ensure the long-term viability and sustainability of their operations, while contributing to the responsible stewardship of our planet’s resources.